Instrument transformers were created to transform voltage from the high values in the transmission and distribution systems to low values that can be utilized by low-voltage devices.
Instrument transformers are used for several primary applications: metering (for energy billing and transaction purposes), protection (for system protection and protective relaying purposes), control (for system control functions) and load survey (for economic management of industrial loads). Depending on the requirements for those applications, the instrument transformer design and construction can be quite different. Generally, metering instrument transformers require high accuracy in the range of normal operating voltage and current. Protection instrument transformers require linearity in a wide range of voltages and currents.
During a disturbance such as a system fault or overvoltage transients, a protective relay uses the instrument transformer’s output to initiate an appropriate action (open or close a breaker, reconfigure the system, etc.) to mitigate the disturbance and protect the rest of the system. Instrument transformers are the most common and economic way to detect such a disturbance.
Outdoor instrument transformers have to perform these functions reliably over many years while being subjected to stress factors such as UV radiation, pollutants, humidity, rain, temperature variations and salt fog. That’s why developers searched for a better material to weather these environmental stresses.
The next generation of outdoor instrument transformers (OIT) was launched in 2004 with new abilities to enhance performance in heavily polluted outdoor environments.
ABB’s new outdoor vacuum circuit recloser (OVR) with hydrophobic cycloaliphatic epoxy (HCEP) embedded poles and vacuum interrupters was the result of an extensive development effort combining the best commercially available outdoor insulation material with advanced design tools and manufacturing processes. The OVR auto-recloser was certified by the South African utility Eskom after it passed the one-year outdoor exposure testing at the Koeberg Insulator Pollution Test Station near Cape Town, South Africa. This location’s climatic conditions have been documented as some of the most severe in the world in terms of damaging UV-radiation, heavy collection of industrial and marine pollutants, and heavy condensation. HCEP embedded poles have also passed fire and smoke tests per French Railways standards.
The success of the OVR recloser with HCEP insulating material led to the development of the next-generation outdoor instrument transformers using the same technological strategy combining advanced design tools with the best commercially available dielectric material.
The Evolution of Outdoor Insulating Materials
In the late 1960s, the prevailing dry type insulating medium for medium-voltage (up to about 40 kV) instrument transformers was butyl rubber. The properly compounded outdoor grade of butyl rubber itself is a very good insulator. However the high processing pressures (more than 15 times the atmospheric pressures) associated with the rubber molding and curing process were not conducive to maintaining the exact clearances and geometries of the core-coil assembly after the molding process. For these reasons, alternative dielectric insulating materials were sought. Proprietary formulations of butyl rubber are still used by some instrument transformer manufacturers.
Liquid casting resins were evaluated and found to be an excellent alternative dielectric to butyl rubbers. Their starting ingredients can be pumped, metered, mixed and dispensed either under moderate vacuum pressures in vacuum casting, or slightly elevated injection pressures (about twice the atmospheric pressures) in automated pressure gelation (APG) process. The curing step is carried out under ambient pressures or slightly elevated pressures of two to three times the atmospheric pressures. These processing conditions better preserve the designed dielectric spacing in the core-coil assembly and yield products with consistent quality.
Cycloaliphatic epoxy (CEP) resin was first introduced in outdoor insulators in the late 1970s based on its very good resistance to degradation and tracking erosion initiated by exposure to humidity, ultraviolet (UV) radiation, outdoor pollutants and chemicals. Its excellent mechanical strength and dielectric properties were also highly desirable for MV equipment. Globally, CEP is the most popular outdoor insulation for medium-voltage equipment. Liquid CEP resins can be processed both by vacuum casting and automated pressure gelation (APG).
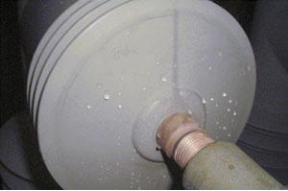
Figure 2. Water beading up on the vertical surface of H2 bushing of the HCEP cast OVR auto-recloser after two years in Kitty Hawk, NC. This demonstrates the hydrophobicity retention of HCEP after prolonged exposure to the coastal environment.
In the 1980s, outdoor grades of polyurethane (PUR) elastomers were found to be another cost-effective insulation for medium-voltage electrical equipment. This liquid-casting resin could be processed mainly by vacuum casting. Among all liquid-casting resins, PUR has the most forgiving process with lower mold temperatures and faster cycle time than vacuum cast epoxy resins. The fully cured PUR elastomers combine desirable properties such as ease of manufacturing (via vacuum casting), mechanical toughness and very good electrical properties. The outdoor grade of PUR has acceptable outdoor performance
Advanced Outdoor Insulation Technology
In outdoor insulation technology today, silicone rubber is widely recognized as the premier material due to a combination of attractive properties, specifically its hydrophobicity (water repelling) properties.
On hydrophilic (water-loving) insulation surfaces, water tends to wet out into a continuous film. Conductive airborne contaminants (e.g., salts, acids, etc.) that collect on these surfaces will dissolve readily in water to form resistive conductive films. These electrolytic films lead directly to dry band arcing. If the insulation is polymeric in nature, arcing can cause erosion of the insulation surface and increase in leakage current. The drying of the remaining part of the insulation surface and subsequent elongation of the arc eventually lead to flashovers. Excessive dry band arcing thus can compromise the outdoor equipment’s long-term performance.
Hydrophobic insulation surfaces, on the other hand, cause water to bead up into droplets, not wet out into a thin film. The droplets can roll off the surface, taking with them any contaminant that collects on it. This is the self-cleaning, or self-washing, characteristic of hydrophobic surfaces. As water cannot wet out readily into a thin conductive film, dry band arcing incidents are reduced. Thus, hydrophobic insulation can extend outdoor equipment life. The result is enhanced reliability of the outdoor product. That is the main reason silicone rubber is the preferred insulation material for high-voltage outdoor insulators.
In the early 2000s, a hydrophobic version of CEP called hydrophobic cycloaliphatic epoxy (HCEP trade name Hydrophobic Araldite) was introduced to the electrical insulating resin market. HCEP purportedly was formulated to sustain some degree of surface hydrophobicity upon prolonged exposure to aggressive outdoor environments without sacrificing other desirable chemical and mechanical properties. Published test data showed that the material exhibits some degree of hydrophobic properties, although not as extensive or as good as those found in silicone rubber.
The HCEP manufacturer has conducted extensive testing of the material and has published many technical papers and reports to demonstrate these hydrophobic property improvements over the baseline CEP while still preserving its excellent electrical, chemical and thermal properties and tracking erosion resistance. Based on this information, HCEP was determined to be the best commercially available outdoor insulation material, and was thus selected for the OVR auto-recloser in 2004.
Advanced Design & Process Technologies
Cost-effective, highly reliable electrical equipment is the result of an optimization process that combines optimum design features with efficient use of the best insulation material available. This approach is utilized in the development of next-generation outdoor instrument transformers. Each insulating material requires its own design of insulating geometry, internal components and manufacturing.
Advanced Design Technologies
Recent availability of advanced simulation software has provided engineers with many tools to develop new products and associated tooling without incurring large prototyping expenses.
For the next generation of instrument transformers, engineers can now use 3D electrostatic simulation software to optimize the outdoor instrument transformer designs. This software calculates electric field stress distribution on the surface and inside the cast electrical device. By varying the insulation material’s dielectric spacing (i.e. the geometry of the design), different field stress distribution can be calculated and therefore optimized to achieve the lowest electric field stresses.
Different insulation materials can be evaluated in the same efficient manner simply by inserting its own dielectric properties into the software for field stress calculations. Furthermore, the environmental conditions surrounding the 3D model of the device can be varied—for example, higher electrical conductivity—to simulate various environmental (climatic) conditions and their effect on field stress distribution.
A good electrical design still needs to lend itself to ease of manufacturing. For resin cast outdoor instrument transformers, mechanical robustness is very important to withstand all the extreme temperature variations. ABB uses extensively a proprietary simulation software called Reactive Molding, RAMZES, for process and mechanical design optimization. The 3D model of the insert design inside a preliminary mold design is first imported into RAMZES. The program then optimizes the process parameters such as mold temperature distribution, mix temperature, filling rate or curing profiles for the resin filling, curing and cooling cycles. It calculates the resulting mechanical stresses and strains that develop inside the cured cast device during the cooling to ambient conditions. Varying the casting and curing parameters yields different stresses and strains in the cooled down device. Processing parameters can then be optimized to yield the lowest stresses and strains in the cast product.
Figure 3. Reactive Molding simulation of 34.5kV outdoor CT – Curing stage
Figure 3 shows an example on how RAMZES was used to optimize the curing stage for the 36-kV CT.
Advanced Process Technologies
The best design utilizing the best material still does not guarantee a reliable and long-lasting performance if the product is not properly manufactured under controlled and repeatable conditions.
Figure 4. Automatic Pressure Gelation (APG) press in ABB’s Pinetops, NC facility.
In the early stages of resin casting technology, vacuum-encapsulating process was most commonly used. This forgiving process allows minimum mechanical reinforcement of the core-coil assembly which is not the case with, for example, the high pressure molding and curing of butyl rubber. One drawback of this process is long total cycle time. Mold filling, curing and demolding usually takes several hours.
During the 1980s, liquid injection casting of epoxies was introduced. The process was further refined and automated with sophisticated controls for consistent results. Today, the automated pressure gelation (APG) effectively shortens the total cycle time to less than 90 minutes and has become the process of choice for epoxies.
Figure 5. Epoxy blending equipment in ABB’s Pinetops, NC facility.
Recognizing the important role of proper manufacturing in producing reliable instrument transformers, it is now possible to install advanced APG casting process equipment along with a state-of-the art automated mix blending and dispensing system. The various ingredients for the epoxy mixture are blended and processed on demand, thereby ensuring that the mixture’s flow properties are optimized for the casting, impregnation of the core-coil assembly and subsequently the curing. The end result is a consistent quality in the finished product.
Conclusion
The new generation of instrument transformers demonstrates a new industry focus on product innovation and advancement in manufacturing technology. Product manufacturers are increasingly performing ongoing evaluations of the long-term performance of new outdoor materials and products, including instrument transformers.
New HCEP products are emerging that provide improved reliability in aggressive outdoor environments, while guaranteeing excellent dielectric and mechanical properties. These features translate into longer life-expectancy, reduced maintenance costs for customers, and ultimately, reduced risk of costly substation power outages.
About the Author:
Hoan Le works with the
ABB Medium Voltage division in Pinetops, N.C. Hoan received his B.S. degree in Chemical Engineering in 1975 from State University of New York at Buffalo and his M.E. degree in Materials Science and Engineering in 1991 from North Carolina State University. He has four patents on electrical insulation systems and several invention disclosures. Hoan is a member of IEEE.
Learn more on website:
http://www.utilityproducts.com.