New Casting System Developed for Medium Voltage Indoor Applications
Epoxy based casting systems for electrical insulation have been in use now for more than 60 years. While many such systems already exist, new ones are still under development in order to meet customer demand for superior technical performance and/or reduced costs. An obvious way to lower cost is to use cheaper materials. However, this risks adversely impacting product performance and reliability. A better approach is to try to lower costs through new ways to optimize the production process.
Traditional material preparation and casting processes for electrical insulation materials can often be complex. Pre-filled materials generally need to be stirred, heated, de-gassed, etc. – all of which take up time and add to costs. INMR recently reported on the development of a new semi-flexible hydrophobic cycloaliphatic epoxy (see INMR Qtr. 2/2010) and its comparatively easy application during production. Now, a similar type of processing concept is being adapted and extended to other casting systems as well.
In this article, contributed by Astrid Beigel and Christian Beisele of Huntsman Advanced Materials in Switzerland, a newly developed casting system for indoor insulation components is presented. This patented system can be applied using simple mixing and dosing equipment and transferred directly from the delivery drum, via a static mixer, into the mold. In addition to saving on both plant and operating costs, it is claimed that this new system – trademarked Cast & Go – ensures very good mechanical as well as electrical properties. Moreover, because of being supplied in in-liner drums, recycling of drums is easy.
_________________________________________________________________________________________________________________________________
Conventional Processing of Epoxy Casting Systems
Traditional application of epoxy-based casting systems often involves numerous steps. For non-prefilled systems, for example, fillers need to be pre-dried at elevated temperature and under vacuum and transferred in the correct proportions to individual pre-mixers. These mixers allow thin-film de-gassing to prepare the filled resins and hardeners. All this requires heat, vacuum and time. After pre-mixing, the resins must be pumped to a metered mixing vessel and then into a pressure pot via a static or dynamic mixer that produces the final curable casting system. The pressure pot must then be disconnected from the mixer and moved to the clamping machine. Finally, the mass is injected at 40 to 60°C into the hot mold (at about 140 °C) using air pressure. After de-molding, parts are normally post-cured in an oven to obtain their full profile of properties.
In the case of pre-filled systems, these can tend to sedimentation and therefore drums must usually be put into an oven for pre-heating. The potentially settled filler is then re-homogenized by stirring in the delivery vessel. After feeding both components into the mixer, resin and hardener have to be de-gassed under both vacuum and temperature before being mixed and applied, as described above.
Processing of the New System
With the new Cast & Go system, resin and hardener are processed directly from their original packaging. As there no need for pre-mixing, pre-heating or degassing of the components, the materials are delivered in straight-sided steel drums with in-liners. This way, uncontaminated drums can be easily recycled.
The resin and hardener are processed in a ratio of 1:1 by volume and desired flow output controlled by a two-component metered mixing machine. The material is then pumped through the static mixer directly into the hot mold. Processing can be carried out even at room temperature although, for high output quantities, it may be advantageous to slightly heat the resin component (50 to 60°C) before injecting into the mold. The mold is typically preheated to between 90°C and 150°C (depending on size of the component to be cast or the volume of the casting) and it is important that only two-component metered mixing equipment is used (as shown in Figure 1) to ensure synchronized dosing of equal volumes of resin and hardener.
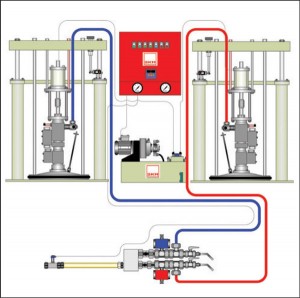
Figure 1: Schematc of mixing and dosing equipment.
Overcoming Development Challenges
Any epoxy casting system that will permit rapid, easy and cost-efficient processing must fulfill certain requirements, as outlined in Table 1. The objective during development of the new system was to achieve all of these.
The biggest challenge in this regard was finding the best balance between sedimentation stability and flow properties. Traditional pre-filled casting systems can not be processed by simple dosing equipment as they are not designed for a 1:1 mixing ratio by volume. The biggest challenge was finding the best balance between sedimentation stability and flow properties. While a simple reformulation to a 1:1 by volume ratio would allow for good flow behavior, it would also result in the filler settling during storage. Such sedimentation could be inhibited by using anti-settling agents but then flowability would be reduced, meaning too long a mold filling time. As a result, developing an entirely new formulation concept was deemed necessary.
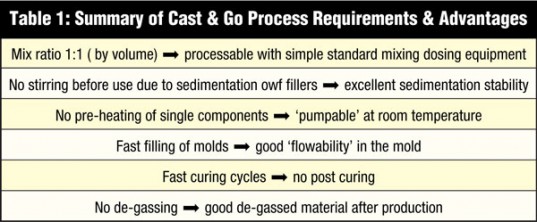
The single components in this formulation would have to possess excellent storage stability and be ‘pumpable’ at room temperature. In addition, the mixture would also have to show good ‘flowability’ under typical molding conditions. The Cast & Go indoor insulation casting system was the result of this development work and offers the following features:
• No preheating necessary (i.e. flows well at room temperature)
• No stirring of sediment required (i.e. stable during storage)
• No homogenizing needed (very storage stable)
• No need for de-gassing (i.e. already well degassed in production)
• No post curing required (i.e. NPC-acceleration concept)
• Pre-filled with Wollastonite (i.e. offers high toughness plus low CTE, meaning excellent thermal cycle crack resistance as well as low abrasion which makes it less damaging to machinery).
Eliminating the Need for Post-Curing
Conventional epoxy casting systems typically undergo a post-curing step after molding. This is because although the strength of the component is already sufficient at time of removal from the mold, the curing reaction is still not fully complete. To achieve full development of all physical properties, the parts must therefore be subjected to a post-curing cycle (i.e. typically 10 hours at 140°C).
In contrast, the new system contains what is referred to as an NPC (i.e. a non-post-cure accelerator package). Using this, the reaction is much faster than for traditional casting so that, even with lower mold temperatures and shorter molding times, curing is virtually complete at time of de-molding. This results in energy savings as well as less time and handling costs.
Computer simulation of degree of conversion at time of de-molding as depicted in Figure 2 compares a traditional casting system with the new system under the same conditions. While the part made using Cast & Go is fully cured, the degree of conversion using a standard system is only 80%.
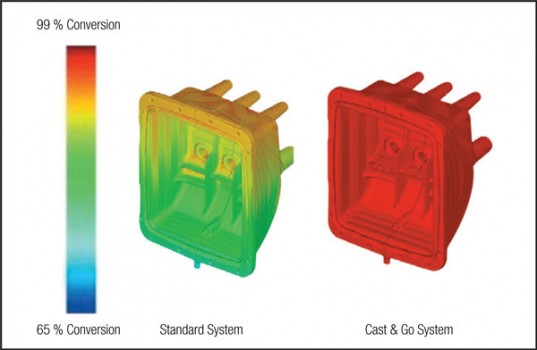
Figure 2: Computer simulation of degree of conversion at time of de-molding.
Comparison with Conventional Systems
In spite of eliminating the need for post-curing, the new casting system yields the same high mechanical values as conventional systems and, in particular, high crack resistance (KIC = 3.0 MPa*m0.5 where KIC is the critical stress intensity factor equaling the resistance against crack initiation – the higher this number, the better) as well as a low coefficient of thermal expansion. This is related to a high proportion of less abrasive (i.e. more equipment-friendly) filler.
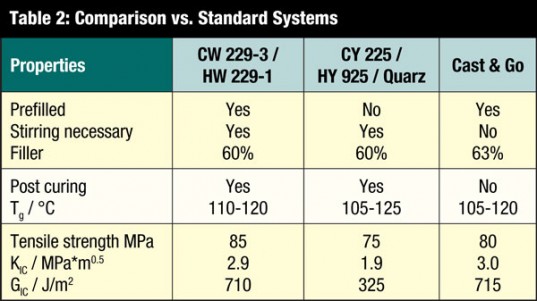
Applications
The new Cast & Go system is designed for use in a range of medium voltage applications including insulators, bushings, switchgear (both SF6 and vacuum type), current instrument transformers and also encapsulation of small motors.
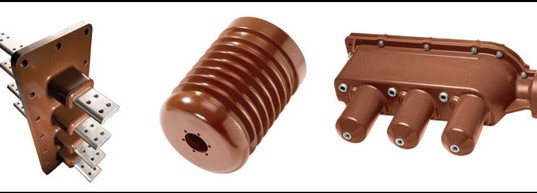
Figure 3: Potential medium voltage application examples for new system.
Initially, it was planned to be used as an APG processing material where maximum fill rates are usually around 4 kg/min. However, during pumping trials at 2KM – the dosing equipment supplier and also Huntsman’s partner in the development of Cast & Go applications – output rates as shown in Table 3 were achieved.
Raising resin temperature by 4°C using a simple electrical heating system resulted in an almost doubling of machine output. By using more efficient heating up to 35°C or 40°C, an output of a high as 15 kg/min would become possible. This level of output was judged more than sufficient to meet the requirements of most customers. For example, Augier in France, has successfully tested Cast & Go for the production of 140 kg parts by a gravity casting process as well as 35 kg parts by the APG process.
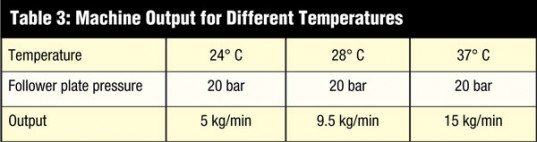
Conclusions
The newly developed Cast & Go system offers several key benefits compared to traditional epoxy casting systems. One of these is the far lower investment cost due to simpler mixing and dosing equipment without need for either pre-heating or curing ovens. Operating costs are also significantly lower due to an easy production process without need for manual preparation of materials. This means improved safety for workers. Moreover, due to the higher reactivity, mold temperature can be reduced, contributing to improved working conditions. Finally, with the possibility to reduce de-molding time by up to 20% compared to conventional systems, there is higher productivity.
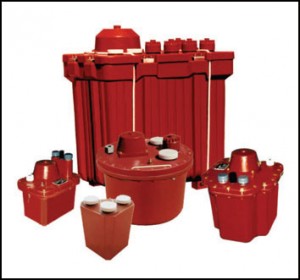
Figure 4: Transformers (in upper portion of photo) from Augier from 0.4 to 32 kVA (5.5 – 6.6 kV) are made using new epoxy system
Although developed for APG applications, the new system has recently even been applied to conventional oven-cured gravity castings. Compared to conventional systems, productivity could increase by up to a factor of 3. Since no pressure pot is necessary using meter mix equipment, there is also no issue of pot life nor is there a need for stirring prior to use.
All these production advantages are complemented by excellent material properties in regard to fracture toughness and coefficient of thermal expansion – meaning parts have a superior thermal cycle crack resistance.
Learn more on website:http://www.inmr.com
【 Go Back 】 | 【 Print 】 | 【 Close this window 】